

The OEM may well change its original design midway through, in which case the contract manufacturer needs a flexible solution. Take the example of a contract manufacturer working with an OEM to develop a new medical device. Robots, which can swiftly respond to modifications, are ideally suited to the task in hand. As products develop, and smaller batch sizes are required, it may be necessary to run different parts through the same production line. On the flip side, traditional automation equipment can be expensive and does not lend itself easily to changes in product design. It tends to be a case where someone would look at either approach and decide which is the most appropriate." Steep incline "Robots tend to be used where you need more flexibility, so it might be lower volume runs. "For the very high-volume end of the business, where you don’t need flexibility, it may be more cost-effective to develop a dedicated automation machine because it can be designed to manufacture the parts very efficiently," explains Wilson.
#Light speed ns verification
This allows original equipment manufacturers (OEMs) to offer complete verification on their products with minimal manpower. A dedicated line is difficult to surpass in terms of speed and productivity: because it has been tailored specifically toward a particular product or part, it guarantees high production rates and reliable quality. Of course, conventional automation solutions are still the best option in many cases. Because flexible automation can be integrated into existing equipment, large and small companies alike now have the means to incorporate robotics into their systems. As YuMi demonstrates, robots are becoming increasingly user-friendly, and automation is beginning to seem attractive even at low order volumes. These days, it appears a tipping point has been reached. While their uses in, say, the automotive sector have never been in doubt, robots were historically viewed as an overly complex way to automate medical device production.
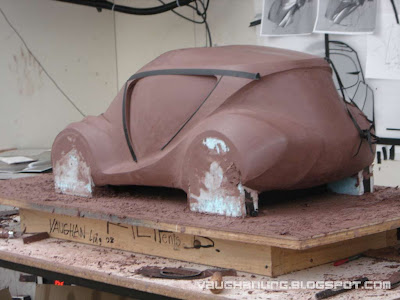
Since then, robotics have made further inroads into the industry. Wilson discussed robots two years ago in this very publication. "Certainly the speed of the robots has increased and their costs have come down, making it easier and more cost-effective to use robots than to build a bespoke piece of machinery." "Across all manufacturing sectors, the design life of the product is becoming shorter," says Mike Wilson, chairman of the British Automation and Robot Association. Today’s manufacturers require more flexibility than ever before, and are finding that traditional solutions aren’t quite up to scratch. But old practices are beginning to shift. For many years, the ‘medtech’ sector made little use of robotics, preferring to stick with the dedicated equipment suited to high volumes of identical parts. While it may take some time before the medical devices industry sees the benefits, robots of this kind seem poised to change the face of automation. Its dexterity, flexibility and agility mean it is particularly suited to small parts assembly in fact, it can perform with sufficient accuracy to thread a needle. To begin with, YuMi – short for ‘you and me’ – will find application in the consumer electronics industry, but it is slated to expand to other market sectors too. When it commercially launches in April 2015, this team-spirited creation by ABB Robotics will be the world’s first collaborative robot. With no need for a safety cage, YuMi can see where it’s going, feel what it’s touching, and deftly navigate its human co-workers. It belongs more in a science fiction film than on a production line: a dual-arm robot that can work together with people on exactly the same tasks. Mike Wilson, chairman of the British Automation and Robot Association, explains how robots are changing the face of medical device production lines.

However, as flexibility becomes more important, manufacturers are seeking solutions that can quickly respond to modifications. High-speed assembly solutions have revolutionised medical device manufacturing, with the move to automation facilitating very high-volume orders.
